
Advanced Marine Riser Inspection & Classification
-
• DNV Certified in accordance with Class Programme DNVGL-CP-0484 (AoSS)
• Purpose designed inspection system based on advanced Phased Array ultrasonic technology.
• Allows complete riser inspection without the requirement of stripping the riser body or removing the riser from stack.
• Performing corrosion and wall thickness mapping on riser main tube and C/K and booster lines.
• Weld inspection of all splice welds on main tube, C/K and booster lines.
-
• Reduced transport and logistics costs due to not needing to send customer equipment.
• Lower risk resulting from reduced transport and handling of large customer equipment.
• Reduced energy consumption and CO2 footprint.
• Reduced downtime for the customer due to portable and efficient inspection.
• Possibility to extend the certification period beyond a 5 calendar-year based period.
• Better inspection and greater integrity assurance for the condition of the equipment
• Environmentally friendly, no use of chemicals during inspection
Technical specification – inspection tools
Main tube corrosion mapping tool
Main tube weld inspection tool
Auxiliary line corrosion mapping tool
Auxiliary line weld inspection tool
Electrical connection 230V
Minimum operating temperature >1dg Celsius
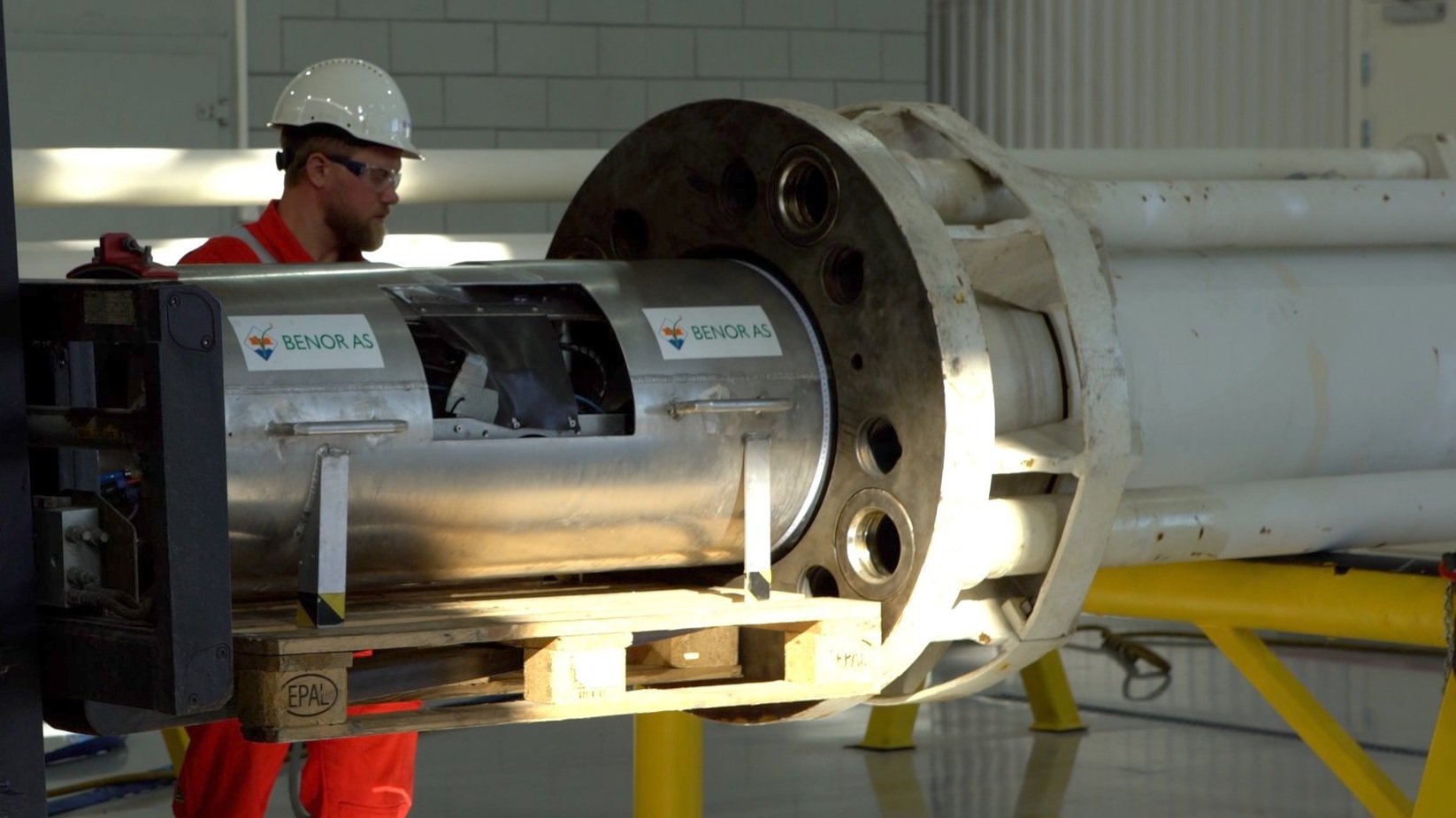
Main tube corrosion & thickness mapping
Main tube corrosion mapping
Custom designed robotic crawler carries a phased array probe through main tube allowing for wall thickness and corrosion mapping.
The probe has an effective range of 25m, utilising a 5Mhz probe with 128 elements.
Main Tube weld inspection
The probe contains an electrically driven weld scanner for main tubes.
Weld scanning is completed by two probes scanning from each side of the weld.
The probe has an effective range of 25m.
Data representation
High resolution visual representations of the scanned data are immediately available clearly identifying areas of concern.
Data is logged and can be analyzed repeatedly for future proofing for regulative changes or weak spots and trends in corrosion.
Auxiliary line inspection
Customized tools for varying auxiliary line dimensions, offering corrosion mapping and weld inspection.
Calibration and sensitivity
Calibration blocks for both main tubes and auxiliary lines contains notches according to DNV acceptance criteria for sensitivity.